Basis for safety and power quality
Grounding and bonding are the basis upon which safety and power quality are built. The grounding system provides a low-impedance path for fault current and limits the voltage rise on the normally non-current-carrying metallic components of the electrical distribution system.
During fault conditions, low impedance results in high fault current flow, causing overcurrent protective devices to operate, clearing the fault quickly and safely. The grounding system also allows transients such as lightning to be safely diverted to earth.
Bonding is the intentional joining of normally non-current-carrying metallic components to form an electrically conductive path. This helps ensure that these metallic components are at the same potential, limiting potentially dangerous voltage differences.
Careful consideration should be given to installing a grounding system that exceeds the minimum NEC requirements for improved safety and power quality.
Recommended practices for grounding
1. Equipment Grounding Conductors
The IEEE Emerald Book recommends the use of equipment-grounding conductors in all circuits, not relying on a raceway system alone for equipment grounding. Use equipment grounding conductors sized equal to the phase conductors to decrease circuit impedance and improve the clearing time of overcurrent protective devices.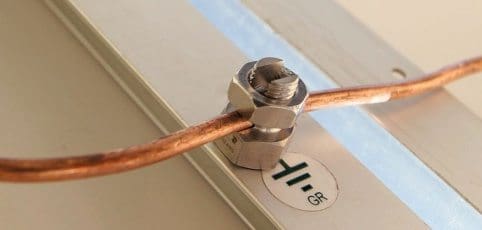
Equipment grounding conductor
The minimum size the equipment grounding conductor for safety is provided in NEC 250.122, but a full-size grounding conductor is recommended for power quality considerations.
Click here for the full article
No comments:
Post a Comment