PLC in adverse conditions
In certain applications, the operating environment may have extreme conditions that require special attention or otherwise can seriously damage PLCs. These adverse conditions include excessive noise and heat and nuisance line fluctuations. This article describes these conditions and provide measures to minimize their effects.1. Excessive Noise
Electrical noise seldom damages PLC components, unless extremely high energy or high voltage levels are present. However, temporary malfunctions due to noise can result in hazardous machine operation in certain applications. Noise may be present only at certain times, or it may appear at widespread intervals. In some cases, it may exist continuously.The first case is the most difficult to isolate and correct.Noise usually enters a system through input, output, and power supply lines. Noise may also be coupled into these lines electrostatically through the capacitance between them and the noise signal carrier lines.
The
presence of high-voltage or long, closely spaced conductors generally
produces this effect. The coupling of magnetic fields can also occur
when control lines are located close to lines carrying large currents.
Devices that are potential noise generators include relays, solenoids, motors, and motor starters, especially when operated by hard contacts, such as push buttons and selector switches.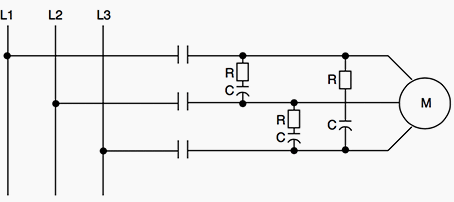
Analog I/O and transmitters are very susceptible to noise from electromechanical sources, causing jumps in counts during the reading of analog data. Therefore, motor starters, transformers, and other electromechanical devices should be kept away from analog signals, interfaces, and transmitters.
Although the design of solid-state controls provides a reasonable amount of noise immunity, the designer must still take special precautions to minimize noise, especially when the anticipated noise signal has characteristics similar to the desired control input signals.
IMPORTANT // To increase the operating noise margin, the controller must be installed away from noise-generating devices, such as large AC motors and high-frequency welding machines.
Also, all inductive loads must be suppressed. Three-phase motor leads
should be grouped together and routed separately from low-level signal
leads.
Sometimes, if the noise level situation is critical, all
three-phase motor leads must be suppressed (see Figure 1 above). Figure
2 illustrates line-filtering configurations used for removing input
power noise to a controller or transmitter.
Note 1 Keep line filters 12 inches or less from the controller. Minimize the line distance where noise can be introduced into the controller.
Note 2 To prevent ground loops, do not tie the common mode line metal case filters with other metal that is at ground potential. Doing so will reduce the filters’ effectiveness.
For the full article, click here