Medium
and high-voltage power cables, in circuits over 2000 volts, usually
have a shield layer of copper or aluminum tape or conducting polymer. If
an unshielded insulated cable is in contact with earth or a grounded
object, the electrostatic field around the conductor will be
concentrated at the contact point, resulting in corona discharge, and
eventual destruction of the insulation.
As well, leakage current and
capacitive current
through the insulation presents a danger of electrical shock. The
grounded shield equalizes electrical stress around the conductor,
diverts any leakage current to ground. Be sure to apply stress relief/
cones at the shield ends, especially for cables operating at more than
2Kv to earth.
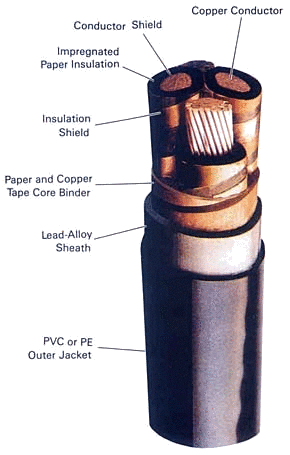
Shields on power cables are connected to earth
ground at each shield end and at splices for redundancy to prevent shock
even though induced current will flow in the shield. This current will
produce losses and heating and will reduce the maximum current rating of
the circuit. Tests show that having a bare grounding conductor adjacent
to the insulated wires will conduct the fault current to earth quicker.
On high current circuits the shields might be connected only at one
end.
On very long high-voltage circuits, the shield may be broken
into several sections since a long shield run may rise to dangerous
voltages during a circuit fault. However, the shock hazard of having
only one end of the shield grounded must be evaluated for the risk!
Shielding
of an electric power cable is accomplished by surrounding the assembly
or insulation with a grounded, conducting medium. This confines the
dielectric field to the inside of this shield.
Two distinct types of shields are used:
The purposes of the insulation shield are to:
- Obtain symmetrical radial stress distribution with the insulation.
- Eliminate tangential and longitudinal stresses on the surface of the insulation.
- Exclude from the dielectric field those materials such as braids, tapes, and fillers that are not intended as insulation.
- Protect
the cables from induced or direct aver-voltages. Shields do this by
making the surge impedance uniform along the length of the cable and by
helping to attenuate surge potentials.
Conductor Shielding
In
cables rated over 2,000 volts, a conductor shield is required by
industry standards. The purpose of the semiconducting, also called
screening, material over the conductor is to provide a smooth cylinder
rather than the relatively rough surface of a stranded conductor in
order to reduce the stress concentration at the interface with the
insulation. Conductor shielding has been used for cables with both
laminar and extruded insulations.
The materials used are either
semiconducting materials or ones that have a high dielectric constant
and are known as stress control materials. Both serve the same function
of stress reduction.
Conductor shields for
paper insulated cables
are either carbon black tapes or metallized paper tapes. The conductor
shielding materials were originally made of semiconducting tapes that
were helically wrapped over the conductor. Present standards still
permit such a tape over the conductor. This is done, especially on large
conductors, in order to hold the strands together firmly during the
application of the extruded semiconducting material that is now required
for medium voltage cables.
Experience with cables that only had a
semi conducting tape was not satisfactory, so the industry changed their
requirements to call for an extruded layer over the conductor.
In
extruded cables, this layer is now extruded directly over the conductor
and is bonded to the insulation layer that is applied over this stress
relief layer. It is extremely important that there be no voids or
extraneous material between those two layers.
Presentday
extruded layers are not only clean (free from undesirable impurities)
but are very smooth and round. This has greatly reduced the formation of
water tress that could originate from irregular surfaces. By extruding
the two layers at the same time, the conductor shield and the insulation
are cured at the same time. This provides the inseparable bond that
minimizes the chances of the formation of a void at the critical
interface. For compatibility reasons, the extruded shielding layer is
usually made from the same or a similar polymer as the insulation.
Special carbon black is used to make the layer over the conductor
semiconducting to provide the necessary conductivity. Industry standards
require that the conductor semiconducting material have a maximum
resistivity of 1,000 meter-ohms. Those standards also require that this
material pass a long-time stability test for resistivity at the
emergency operating temperature level to insure that the layer remains
conductive and hence provides a long cable life.
A
water-impervious material can be incorporated as part of the conductor
shield to prevent radial moisture transmission. This layer consists of a
thin layer of aluminum or lead sandwiched between semiconducting
material. A similar laminate may be used for an insulation shield for
the same reason.
There is no definitive standard that describes the class of extrudable shielding materials known as “
super smooth, super clean”.
It is not usually practical to use a manufacturer’strade name or
product number to describeany material. The term “super smooth, super
clean” is the only way at this writing to describe a class of material
that provides a higher quality cable thanan earlier version. This is
only an academic issue since the older type of materials are no longer
used for medium voltage cable construction by known suppliers. The point
is that these newer materials have tremendously improved cable
performance in laboratory evaluations.
Insulation Shielding For Medium-Voltage Cables
The insulation shield for a medium voltage cable is made up of two components:
- Semiconducting or stress relief layer
- Metallic layer of tape or tap , drain wires, concentric neutral wires, or a metal tube.
They must function as a unit for a cable to achieve a long service life
Stress Relief Layer
The
polymer layer used with exbuded cables has replaced the tapes shields
that were used many years ago. This extruded layer is called the
extruded insulation shield or screen. Its properties and compatibility
requirements are similar to the conductor shield previously described
except that standards require that the volume resistivity of
this external layer be limited to 500 meter-ohms.
The nonmetallic
layer is directly over the insulation and the voltage stress at that
interface is lower than at the conductor shield interface.. This outer
layer is not required to be bonded for cables rated up to 35 kV. At
voltages above that, it is strongly recommended that this layer be
bonded to the insulation .
Since most users want this layer to be easily removable, the
Association of Edison Illuminating Companies
(AEIC) has established strip tension limits. Presently these limits are
that a 1/2 inch wide strip cut parallel to the conductor peel off with a
minimum of 6 pounds and a minimum of 24 pounds of force that is at a
90º angle to the insulation surface.
Metallic Shield
The
metallic portion of the insulation shield or screen is necessary to
provide a low resistance path for charging current to flow to ground. It
is important to realize that the extruded shield materials will not
survive a sustained current flow of more than a few milliamperes. These
materials are capable of handing the small amounts of charging current,
but cannot tolerate unbalanced or fault currents.
The metallic component of the
insulation shield
system must be able to accommodate these higher currents. On the other
hand, an excessive amount of metal in the shield of a single-conductor
cable is costly in two ways. First, additional metal over the amount
that is actually required increases the initial cost of the cable.
Secondly, the greater the metal component of the insulation shield, the
higher the shield losses that result h m the flow of current in the
central conductor.
A sufficient amount of metal must be provided
in the cable design to ensure that the cable will activate the back-up
protection in the event of any cable fault over the life of that cable.
There is also the concern for shield losses.
It therefore becomes essential that:
- The
type of circuit interrupting equipment to be analyzed.What is the design
and operational setting of the hse, recloser, or circuit breaker?
- What fault current will the cable encounter over its life?
- What
shield losses can be tolerated? How many times is the shield to be
grounded? Will there be shield breaks to prevent circulating currents?
Concentric Neutral Cables
When
concentric neutral cables are specified, the concentric neutrals must
be manufactured in accordance with ICEA standards. These wires must meet
ASTM B3 for uncoated wires or
B33 for coated wires.
These
wires are applied directly over the nonmetallic insulation shield with a
lay of not less than six or more than ten times the diameter over the
concentric wires.
Shielding Of Low Voltage Cables

Shielding
of low voltage cables is generally required where inductive
interference can be a problem. In numerous communication,
instrumentation, and control cable applications, small electrical
signals may be transmitted on the cable conductor and amplified at the
receiving end. Unwanted signals (
noise) due to
inductive interference can beaslargeasthedesiredsignal. This can result
in false signals or audible noise that can effect voice communications.
Across
the entire frequency spectrum, it is necessary to separate disturbances
into electric field effects and magnetic field effects.
Electric Fields
Electric
field effects are those which are a function of the capacitive coupling
or mutual capacitance between the circuits. Shielding can be effected
by a continuous metal shield to isolate the disturbed circuit fiom the
disturbing circuit.
Even semiconducting extrusions or tapes
supplemented by a grounded dmin wire can serve some shielding function
for electric field effects.
Magnetic Fields
Magnetic field
effects are the result of a magnetic field coupling between circuits.
This is a bit more complex thanfor electrical effects.
At
relatively low frequencies, the energy emitted from the source is
treated as radiation. This increases with the square of the frequency.
This electromagnetic radiation can cause dislxrbancesat considerable
distance and will penetrate any “openings” in the shielding. This can
occur with braid shields or tapes that are not overlapped. The type of
metal used in the shield also can effect the amount of disturbance.
Any
metallic shield material, as opposed to magnetic metals, will provide
some shield due to the eddy currents that are set up in the metallic
shield by the impinging field. These eddy currents tend to neutralize
the disturbing field. Non-metallic, semiconducting shielding is not
effective for magnetic effects. In general, the most effective shielding
is a complete steel conduit, but thisis not always practical.
The effectiveness of a shield is called the “
shielding factor” and is given as:
SF = Induced voltage in shield circuit / Inducted voltage in unshielded circuit
Test
circuits to measure the effectiveness of various shielding designs
against electrical field effects and magnetic field effects have been
reported by Gooding and Slade.